Welcome to our Blog!
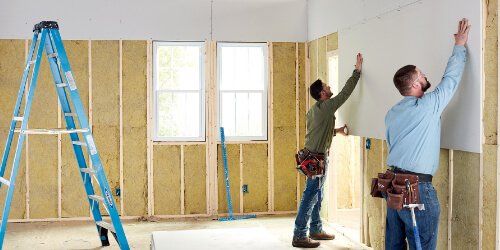
Drywall is a staple in modern construction, providing a smooth, durable surface for walls and ceilings. However, many homeowners are unaware of the impact drywall can have on indoor air quality (IAQ). In Regina, Saskatchewan, where residents often spend significant time indoors during harsh winters, maintaining good IAQ is crucial. Let’s explore how drywall influences air quality and what steps you can take to ensure a healthy indoor environment. How Drywall Affects Indoor Air Quality 1. Off-Gassing from Drywall Materials Some drywall products, particularly those made with synthetic gypsum or certain additives, may release volatile organic compounds (VOCs). VOCs can contribute to indoor air pollution, causing symptoms like headaches, allergies, or respiratory irritation in sensitive individuals. 2. Mold and Mildew Growth When exposed to excessive moisture, drywall can become a breeding ground for mold and mildew. Mold spores released into the air can significantly degrade IAQ and trigger health problems, including asthma and allergic reactions. 3. Dust from Installation and Repairs Drywall installation and sanding can generate fine dust particles, which, if not properly managed, can linger in the air. Inhaling these particles may irritate the respiratory system and exacerbate conditions like asthma. 4. Eco-Friendly Drywall Options Advancements in drywall technology have introduced eco-friendly options that are low in VOCs and designed to resist mold growth. Choosing these materials can help maintain better IAQ while still providing the durability and aesthetics of traditional drywall. Tips to Improve Indoor Air Quality with Drywall 1. Choose High-Quality Materials Opt for drywall products certified for low VOC emissions, such as GreenGuard Gold or similar certifications. These materials are specifically designed to reduce indoor air pollution. 2. Control Moisture Levels Prevent mold growth by controlling indoor humidity levels. Use dehumidifiers in basements and other moisture-prone areas, and promptly address leaks or water damage. Consider moisture-resistant drywall in areas like bathrooms and laundry rooms. 3. Proper Ventilation During Installation Ensure adequate ventilation during drywall installation or repairs. Open windows, use fans, and consider wearing protective masks to minimize dust exposure. 4. Regular Maintenance Inspect your drywall regularly for signs of damage or moisture. Address any issues immediately to prevent mold and structural problems. 5. Professional Installation Hire experienced drywall contractors, like Regina Drywallers, to ensure proper installation techniques are used. Professionals can minimize dust generation and ensure the materials used are suitable for your home. Signs of Poor Indoor Air Quality If you suspect that drywall is impacting your IAQ, watch for these common signs: Persistent Musty Odors: Could indicate mold growth behind walls. Visible Mold or Mildew: Spots or discoloration on drywall surfaces. Allergy-Like Symptoms: Sneezing, coughing, or itchy eyes when indoors. Excess Dust: Accumulation of fine particles on surfaces near recently installed or sanded drywall. How Regina Drywallers Can Help At Regina Drywallers, we are committed to ensuring your drywall enhances your living space without compromising air quality. Our services include: Eco-Friendly Material Options: We source low-VOC and moisture-resistant drywall tailored to your needs. Expert Installation: Minimize dust and ensure proper handling of drywall to protect your IAQ. Repairs and Mold Mitigation: Address water damage and remove mold-affected drywall to restore a healthy environment. Conclusion Drywall plays a critical role in shaping the look and feel of your home, but its impact on indoor air quality should not be overlooked. By selecting the right materials, maintaining your walls, and working with professionals like Regina Drywallers , you can enjoy the benefits of beautiful, functional walls without sacrificing a healthy indoor environment. If you're ready to upgrade your home's drywall or need expert advice on maintaining IAQ, contact Regina Drywallers today!
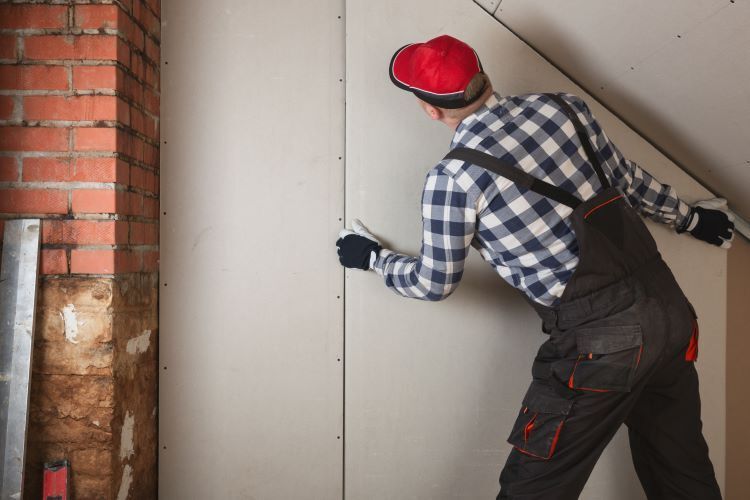
Installing drywall is a critical step in creating smooth, finished walls, whether for a new construction project or a renovation. Proper preparation ensures the drywall installation process goes smoothly, resulting in a professional and long-lasting finish. At Regina Drywallers, we’ve mastered the art of drywall installation and know the importance of thorough preparation. Here’s a step-by-step guide to getting your walls ready for drywall installation . Step 1: Clear the Workspace A clean and organized work area is essential for safe and efficient drywall installation. What to do: Remove furniture, decor, and personal belongings from the room. Cover the floors with drop cloths to protect them from dust and debris. Ensure there’s adequate lighting and ventilation in the workspace. Tip: Use plastic sheeting to seal off the area to minimize dust spreading to other parts of your home. Step 2: Inspect and Repair the Framing The framing provides the foundation for drywall. Any issues with the framing can affect the stability and appearance of the finished walls. Steps to follow: Check studs and joists to ensure they’re straight, level, and properly spaced (typically 16 or 24 inches apart). Secure any loose framing with nails or screws. Replace damaged or warped wood to ensure a flat surface for drywall installation. Tip: Use a level to verify that all framing components are aligned correctly. Step 3: Install Electrical and Plumbing Components Ensure all behind-the-wall systems are completed and inspected before covering them with drywall. Tasks to complete: Run electrical wiring, plumbing pipes, and HVAC ducts. Install outlet boxes and light switches, ensuring they protrude enough to align with the drywall surface. Have the work inspected by a professional to confirm compliance with local building codes. Tip: Take photos of the wall interiors before installation to document the placement of wires and pipes for future reference. Step 4: Apply Insulation and Vapor Barriers Adding insulation improves energy efficiency, and vapor barriers help prevent moisture buildup. Steps to take: Insert insulation between studs to achieve desired thermal or soundproofing effects. Install vapor barriers in areas prone to moisture, such as basements or bathrooms. Secure insulation with staples or fasteners to ensure it stays in place. Tip: Choose insulation materials suited to Regina’s climate for optimal performance. Step 5: Check for Obstructions and Protrusions Before attaching drywall, ensure the wall surface is free of obstacles. What to do: Remove nails, screws, or debris from studs. Trim any protruding nails or wood fragments. Mark the locations of studs, electrical boxes, and pipes on the floor or ceiling for easy reference during drywall installation. Tip: Use a stud finder or laser level for precise measurements. Step 6: Gather the Necessary Tools and Materials Having all tools and supplies ready ensures a seamless installation process. Essentials include: Drywall panels of appropriate size and thickness. Screws, nails, and a screw gun or drill. Tape measure, utility knife, and T-square. Drywall lift or support for handling large panels. Tip: Consult your drywall contractor to confirm the best materials for your specific project. Conclusion Proper wall preparation is the foundation of a successful drywall installation. By following these steps, you’ll ensure a smooth process and a durable, professional finish. If you’re ready to transform your space, trust Regina Drywallers for expert drywall installation services in Regina, Saskatchewan. Contact us today to discuss your project and learn how we can bring your vision to life!
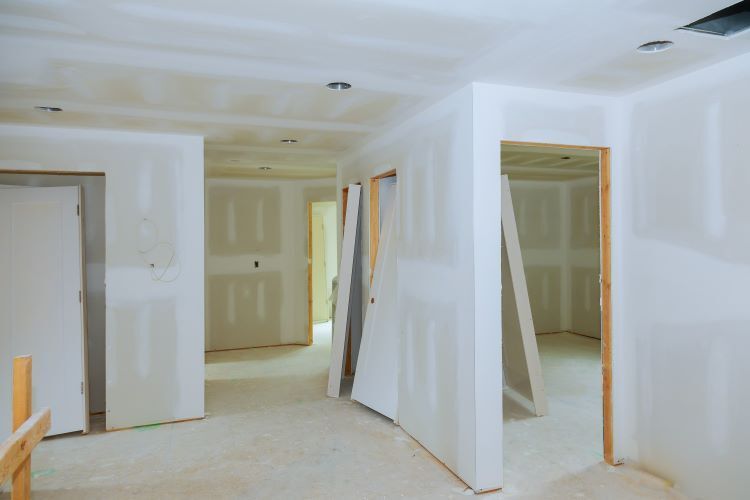
When it comes to drywall installation , not all materials are created equal. Whether you're renovating your home, finishing a basement, or constructing a new commercial space, the type of drywall you choose can significantly impact the overall durability, soundproofing, and appearance of your walls. At Regina Drywallers , we recommend solid gypsum sheets as the ultimate choice for superior drywall performance. Let's explore why solid gypsum sheets are a top-tier option for your next project in Regina, Saskatchewan. What Are Solid Gypsum Sheets? Solid gypsum sheets, commonly referred to as drywall, wallboard, or plasterboard, are panels made of a non-combustible gypsum core encased in a layer of paper. Gypsum is a mineral known for its strength, fire resistance, and moisture-absorbing properties, making it an ideal material for interior walls and ceilings. Unlike traditional plaster walls, solid gypsum sheets are easier to install, repair, and finish, making them a popular choice in modern construction. The Advantages of Choosing Solid Gypsum Sheets 1. Superior Durability and Strength One of the most significant benefits of solid gypsum sheets is their durability. These sheets are designed to withstand the daily wear and tear that walls typically endure, especially in high-traffic areas. Whether you have an active household with kids and pets or a busy commercial space, solid gypsum sheets offer exceptional resistance to dents, scratches, and impacts. Ideal for Homes and Businesses : Perfect for residential and commercial properties, these sheets maintain their structure and appearance for years. 2. Excellent Fire Resistance Safety is a top priority in any construction project, and solid gypsum sheets are renowned for their fire-resistant properties. The core of gypsum contains water molecules that, when exposed to high temperatures, release water vapor, effectively slowing down the spread of flames. Code Compliance : Using fire-rated gypsum sheets can help your building meet local fire safety codes and standards. Enhanced Safety : Ideal for walls and ceilings in kitchens, garages, and other areas where fire hazards are more likely. 3. Moisture and Mold Resistance For areas prone to moisture, such as basements, bathrooms, and kitchens, choosing the right drywall is crucial. Solid gypsum sheets are available in moisture-resistant varieties, often referred to as "green board" or "purple board." These are specifically designed to prevent water damage and inhibit the growth of mold and mildew. Long-Lasting Protection : Protects walls from the damaging effects of humidity and water exposure. Healthy Indoor Air Quality : Reduces the risk of mold-related health issues by preventing mold spores from spreading. 4. Soundproofing Capabilities If you're looking to create a peaceful, noise-free environment, solid gypsum sheets can help. They offer excellent soundproofing properties, making them an ideal choice for bedrooms, offices, and entertainment rooms. For even greater sound reduction, consider using thicker gypsum sheets or adding a layer of sound-dampening insulation. Privacy and Comfort : Reduces noise transmission between rooms, enhancing privacy and comfort. Perfect for Multi-Unit Buildings : Great for condos, apartments, and shared office spaces where sound control is essential. 5. Ease of Installation and Finishing Solid gypsum sheets are known for their ease of installation. They can be quickly cut to size, making them a versatile option for various wall and ceiling configurations. Additionally, gypsum sheets provide a smooth, even surface that’s easy to paint, wallpaper, or texture, allowing you to achieve your desired aesthetic. Time and Cost Efficiency : Gypsum drywall installation is faster and more cost-effective than traditional plastering. Versatile Design Options : Supports a wide range of finishes to suit your interior design needs. When to Use Solid Gypsum Sheets Solid gypsum sheets are suitable for a variety of applications, making them an excellent choice for both new construction and renovation projects. Here are some common uses: Residential Homes : Ideal for creating smooth, finished walls and ceilings in living rooms, bedrooms, and hallways. Basement Renovations : Moisture-resistant gypsum sheets are perfect for finishing basements, protecting against dampness and mold. Commercial Spaces : Durable and fire-resistant sheets are ideal for office buildings, retail stores, and restaurants. Soundproofing Projects : Use thicker gypsum sheets for home theaters, recording studios, or shared walls in multi-family units. Tips for Maintaining Solid Gypsum Drywall To get the most out of your solid gypsum drywall, regular maintenance is key. Here are some quick tips to keep your walls looking their best: Perform Regular Inspections : Check for cracks, dents, or moisture damage, especially in high-traffic areas. Clean Walls Gently : Use a soft cloth and mild detergent to clean your walls without damaging the surface. Address Repairs Quickly : Small holes or dents can be easily repaired with joint compound and sanding. For larger issues, consider hiring professionals like Regina Drywallers for a seamless fix. Repaint as Needed : Fresh paint can rejuvenate your space and protect your walls from daily wear and tear. Why Choose Regina Drywallers for Your Drywall Needs? At Regina Drywallers , we specialize in providing top-quality drywall services throughout Regina, Saskatchewan. Whether you’re building a new home, renovating an existing space, or updating your commercial property, we have the expertise to deliver exceptional results. Here’s why you should choose us: Experienced Professionals : Our team has years of experience in drywall installation, repair, and finishing. High-Quality Materials : We use only the best solid gypsum sheets to ensure durability and longevity. Customer Satisfaction : We are committed to providing exceptional customer service and tailored solutions to meet your specific needs. Final Thoughts Solid gypsum sheets offer a range of benefits, from superior durability and fire resistance to moisture protection and soundproofing. Whether you're a homeowner looking to renovate your space or a business owner aiming to enhance your property, choosing the right drywall material is essential for long-term satisfaction. Ready to upgrade your walls with solid gypsum sheets? Contact Regina Drywallers today for expert advice and professional drywall services in Regina, Saskatchewan. Let us help you achieve flawless walls that stand the test of time!
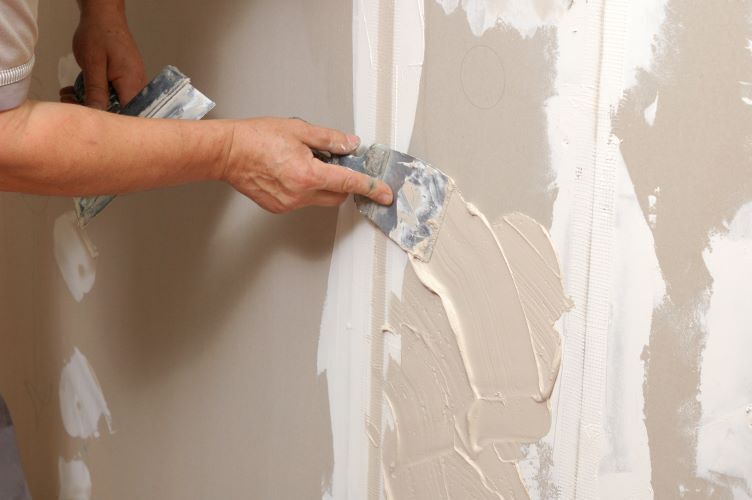
Drywall finishing is one of the most critical stages of a drywall installation project. While installing drywall is an important step, it’s the finishing process that really brings the walls and ceilings to life, creating a smooth, seamless surface ready for paint or other finishes. Whether you’re renovating a home, finishing a basement, or working on a commercial property, understanding the drywall finishing process is key to achieving the best results. At Regina Drywallers , we have years of experience providing top-quality drywall finishing services to homeowners and businesses across Regina. In this blog post, we’ll walk you through the drywall finishing process step-by-step so you know exactly what to expect and how to prepare for each phase of the job. Step 1: Taping the Seams Once drywall sheets have been securely mounted on the walls or ceiling, the first step in the finishing process is taping the seams. This involves covering the joints where the drywall sheets meet with a special drywall tape and compound. Materials used : Paper tape or mesh tape Procedure : The drywall compound (also known as joint compound or mud) is applied to the seams with a drywall knife, and then the tape is embedded into the wet compound. This helps reinforce the joints and prevent cracking. Why it matters : Taping ensures that the seams are properly sealed and creates a smooth base for the subsequent layers of finishing. Step 2: Applying the First Coat of Joint Compound After the seams are taped, the next step is to apply the first coat of joint compound. This is the first layer of mud that covers the tape and fills in the gaps between the drywall sheets. Procedure : A wide drywall knife or trowel is used to spread the compound evenly over the taped seams and along any screw or nail heads. The goal is to create a smooth, consistent layer over the tape, blending it into the surrounding drywall surface. Why it matters : This first layer helps create a solid foundation and smooth out the rough seams created by the drywall installation process. It also fills in any imperfections like nail pops or small gaps between sheets. Step 3: Sanding and Smoothening Once the first coat of joint compound has dried (which usually takes about 24 hours), it’s time to sand the surface. This step is crucial for ensuring that the drywall has an even, smooth finish, free of lumps or ridges. Procedure : A drywall sander or a hand sanding block is used to smooth out the dried compound. Sanding is typically done in a circular motion to remove excess mud and create a smooth, flat surface. Why it matters : Proper sanding is essential to achieving a flawless surface, as it ensures there are no bumps or imperfections that could affect the final finish. Step 4: Applying the Second Coat of Joint Compound Once the surface is smooth, a second coat of joint compound is applied to further smooth out the seams, cover any imperfections, and enhance the overall appearance of the drywall. Procedure : Similar to the first coat, the second layer of compound is spread over the seams, filling in any remaining gaps or uneven areas. This coat is typically thinner and more refined than the first coat, as it’s meant to create a perfectly smooth finish. Why it matters : The second coat helps create a seamless look, ensuring that the drywall joints are barely visible and that the compound fills in all of the gaps. Step 5: Final Sanding and Touch-Ups After the second coat of compound has dried, it’s time for another round of sanding to achieve a perfectly smooth surface. This is followed by any necessary touch-ups. Procedure : The surface is lightly sanded to remove any minor imperfections. If needed, a third thin coat of joint compound is applied and sanded again for an ultra-smooth finish. At this stage, the drywall should look flawless with no visible seams or imperfections. Why it matters : This final sanding and touch-up step is critical for ensuring that the drywall is ready for priming and painting. A smooth, flawless finish is essential to achieving a professional look when the walls are painted. Step 6: Priming and Painting Once the drywall finishing is complete, the next step is priming and painting the surface. Priming prepares the drywall for paint by sealing the surface and helping the paint adhere better, while also hiding any remaining seams or imperfections. Procedure : A drywall primer is applied first, followed by a paint finish of your choice. The type of paint used can vary depending on the room’s purpose (e.g., bathroom, kitchen, or living room) and the desired aesthetic. Why it matters : Priming and painting complete the drywall finishing process, providing both functional protection and an aesthetically pleasing look for your space. Why Choose Regina Drywallers for Your Drywall Finishing? At Regina Drywallers , we pride ourselves on delivering high-quality drywall finishing that ensures a professional, flawless result. Our team has years of experience in the industry, and we take the time to carefully complete every step of the drywall finishing process. Whether you’re renovating a basement or finishing a new construction, we offer the expertise you need to transform your space. Our commitment to quality, attention to detail, and use of top-notch materials ensures that your drywall finishing will be smooth, seamless, and built to last. Conclusion Drywall finishing is a detailed and skilled process that requires careful attention to detail at every stage. From taping and mudding the seams to the final coat of paint, each step is essential to achieving the smooth, flawless finish that every homeowner desires. With the right tools, technique, and experience, drywall finishing can transform a bare, unfinished space into a polished, inviting area. If you're planning a drywall project in Regina, trust the experts at Regina Drywallers to deliver top-quality results. Contact us today to learn more about our drywall finishing services or to get started on your next home renovation!
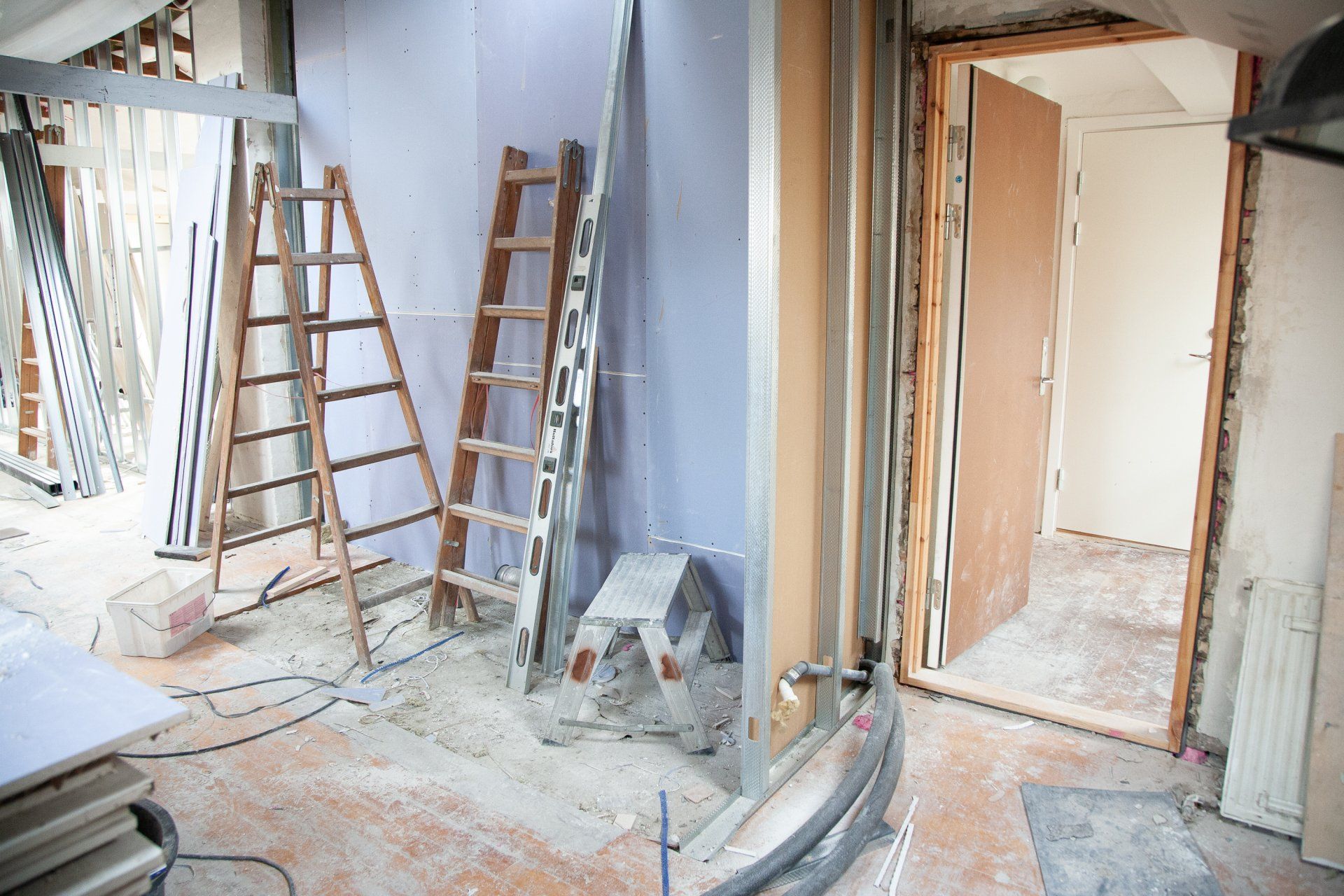
Drywall repair can range from small patch-ups to more extensive repairs, especially after minor accidents, water damage, or home improvements. Whether you’re tackling it as a DIY project or just want to be informed about what a professional repair entails, having the right supplies on hand makes all the difference in achieving a seamless finish. At Regina Drywallers, we know the ins and outs of drywall repair and want to share the essentials with you. Here’s your complete checklist for a smooth, effective drywall repair . 1. Patching Compound or Spackle Purpose: Patching compound, often known as spackle, is the cornerstone of drywall repair. It fills holes, dents, and minor imperfections, providing a smooth, even surface for painting. Recommendation: Opt for a high-quality spackle that’s easy to sand and doesn’t shrink as it dries. For larger holes, joint compound is typically more effective due to its thicker consistency. 2. Drywall Repair Patch or Mesh Tape Purpose: Fo r holes larger than nail or screw punctures, a drywall repair patch or mesh tape is necessary. These products reinforce the damaged area, providing a firm foundation to hold the compound. Recommendation: Self-adhesive fiberglass mesh tape is ideal for medium-sized holes, while metal or aluminum patches are best for larger holes. Make sure to measure the hole beforehand to get the correct size. 3. Putty Knife Purpose: A putty knife is used to apply spackle, joint compound, or patching compound, helping you to spread it smoothly over the repair area. Recommendation: Keep a few sizes on hand, like a 2-inch knife for small holes and a 6-inch or 12-inch knife for larger repairs. Stainless steel blades work well for easy cleaning and a smoother finish. 4. Sandpaper and Sanding Block Purpose: Sanding is essential for achieving a flat, seamless finish. Sandpaper helps smooth out compound edges, making the patched area blend in with the surrounding wall. Recommendation: Use a sanding block for better control and even pressure. For drywall repair, start with medium-grit sandpaper (120-150 grit) for initial smoothing, then move to finer grit (220 grit) for a polished finish. 5. Utility Knife Purpose: A utility knife is a versatile tool for drywall repairs, ideal for cutting drywall patches, trimming excess compound, and smoothing edges. Recommendation: Invest in a high-quality utility knife with replaceable blades. A sharp blade reduces tearing and produces cleaner cuts, which is crucial for patching holes seamlessly. 6. Primer Purpose: Primer preps the repaired surface for paint, ensuring the patch blends smoothly and doesn’t stand out from the rest of the wall. Recommendation: Choose a stain-blocking primer for areas that have been damaged by water or smoke. For smaller repairs, a spray primer can work well for a quick application. 7. Paint Matching the Existing Wall Color Purpose: Once the repair is finished, painting over it with a matching color completes the seamless look. Recommendation: If you don’t have leftover paint, many hardware stores offer color-matching services. It’s essential to blend the color as closely as possible to avoid noticeable patches. 8. Dust Mask or Respirator Purpose: Sanding drywall produces fine dust that can irritate your respiratory system, making a dust mask or respirator essential for safe, dust-free breathing. Recommendation: Use a high-quality, well-fitted mask with a filtration rating, like N95, to protect yourself from dust particles. 9. Drop Cloths or Plastic Sheeting Purpose: Repairs, sanding, and painting can be messy, so protecting your floor and furniture with drop cloths or plastic sheeting is important. Recommendation: Cloth drop cloths are durable and reusable, while plastic sheeting is more lightweight and disposable. Either option works to keep your space clean and protected. 10. Drywall Saw (Optional) Purpose: For larger repairs where a full patch is needed, a drywall saw can help cut out damaged areas cleanly. Recommendation: Use a drywall-specific saw, which is typically compact and serrated for more controlled cuts. Electric multi-tools with drywall blades can also work well for larger projects. Additional Tips for Seamless Drywall Repair Layer Your Compound: Apply multiple thin layers of compound rather than one thick one. This helps prevent cracking and makes sanding easier. Feather the Edges: When spreading compound, feather the edges outward to blend the patch with the wall seamlessly. Check for Imperfections: After sanding, shine a light across the patch to reveal any imperfections. A quick touch-up at this stage can save time and create a smoother result. Allow for Adequate Drying: Compound and primer both need ample drying time to avoid issues with the final finish. Final Thoughts Whether you’re fixing small dents or patching larger holes, having the right supplies on hand makes drywall repair more manageable and leads to a much better outcome. At Regina Drywallers , we understand that each repair job is unique, and we’re here to help ensure your walls look as good as new. With this checklist, you’ll be well-prepared for any drywall repair project that comes your way!
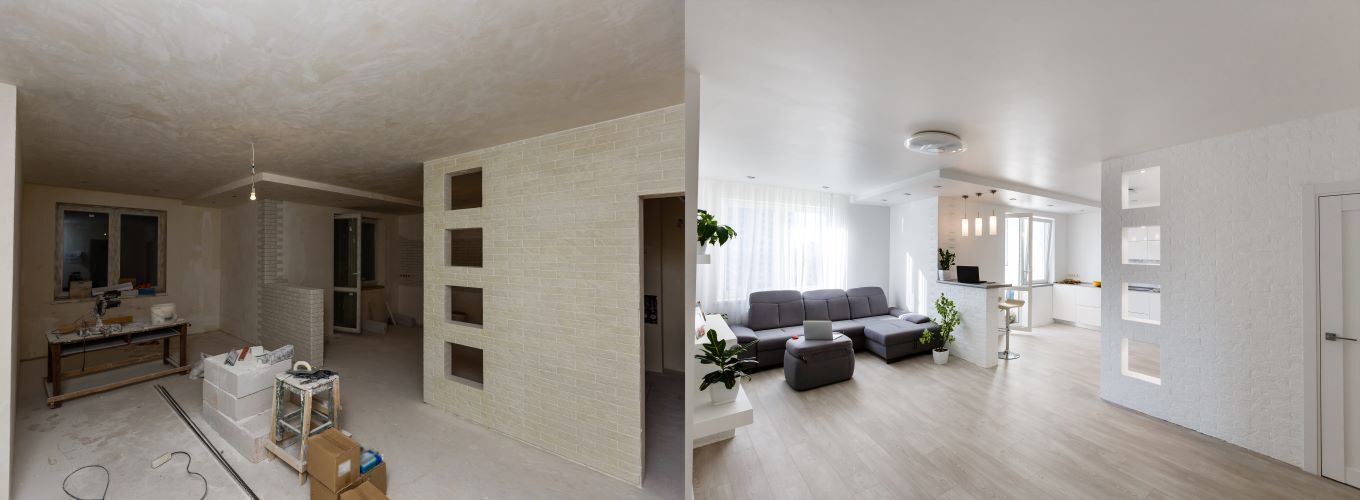
Drywalling is one of the most crucial steps in any basement renovation. It transforms bare walls into smooth, finished surfaces, setting the stage for further design and functionality. But how long does it actually take to drywall a basement? This timeline can vary based on several factors, such as the size of your basement, the complexity of the layout, and the skill level of the crew handling the job. In this guide, we’ll cover the essential steps involved in drywalling a basement , average timeframes for each, and tips for making the process as efficient as possible. Step 1: Planning and Preparation Before the first sheet of drywall goes up, there’s a bit of planning and preparation involved. This step includes taking measurements, ordering the correct amount of drywall sheets, and gathering necessary materials like insulation, corner beads, and joint compound. If any additional prep work is needed, such as framing adjustments or applying moisture-resistant barriers, that should also be completed before the drywall installation begins. Average Time: 1-2 Days Step 2: Insulation and Moisture Protection Insulating your basement walls is essential for maintaining a comfortable temperature and preventing mold growth. Adding a moisture barrier may also be necessary in basements where humidity is a concern, particularly in regions like Regina, where winters can be harsh. Moisture-resistant drywall, also known as green board, is another option, especially for basements with a higher risk of moisture intrusion. Average Time: 1 Day Step 3: Installing Drywall Panels This is the stage where your basement starts to take shape. Drywall panels are carefully installed on the framed walls, with each sheet secured with screws. If your basement has intricate layouts, such as alcoves or utility access panels, these areas may require custom cutting and fitting, which can add time to the installation process. For a standard basement, drywalling typically involves two installers, one to position and secure the sheets and another to support and pass the sheets into place. Depending on the complexity of the layout and the size of the basement, this phase can take anywhere from a day to a few days. Average Time: 2-3 Days Step 4: Taping and Mudding After the drywall sheets are secured, the seams between each sheet must be taped and covered with joint compound, or "mud." This step ensures a smooth finish and hides any seams, screws, or imperfections. In most cases, multiple layers of compound are required, with drying time in between each coat. This step requires patience to allow the compound to dry fully, especially in colder or more humid environments that can slow down drying time. For most basements, applying and sanding down the layers of mud takes around three days, allowing 24 hours of drying time between each layer. If you’re after a particularly smooth finish, an additional coat and sanding session may be necessary. Average Time: 3-5 Days Step 5: Sanding and Priming Once the compound is fully dry, the surface must be sanded to create a smooth, even finish. Sanding helps remove any bumps or rough spots, making it easier to achieve a professional-looking finish. After sanding, a primer is applied to prepare the walls for painting. Primer helps paint adhere better to drywall and provides an even base for the final color. Average Time: 1-2 Days Step 6: Final Inspection and Touch-Ups Before calling the project complete, a final inspection ensures that every surface is smooth, every corner is sharp, and there are no visible imperfections. Any areas that need touch-ups will be re-sanded, re-taped, or re-mudded as necessary. While this may seem minor, attention to detail here is crucial to achieving that polished, professional look. Average Time: 1 Day Total Time Estimate: 7-10 Days On average, drywalling a standard-sized basement takes around 7-10 days, assuming each step proceeds smoothly and there are no unexpected delays. Larger basements or basements with complex layouts can take up to two weeks, while smaller, straightforward layouts may be completed in less than a week. Factors That Can Affect the Timeline Basement Size and Layout: Larger basements or those with non-standard layouts require more time for measuring, cutting, and securing drywall sheets. Moisture Conditions: In cases where moisture is a concern, additional time may be needed to apply moisture-resistant materials or sealants. Weather and Drying Times: Humidity and cold can slow drying times for joint compound, potentially extending the timeline. Experience of the Installers: Experienced professionals work more efficiently and avoid errors that might require rework. Additional Customizations: Special features, like alcoves or recessed lighting, may add to the time due to custom cutting and installation requirements. How to Speed Up the Drywalling Process If time is a priority, there are ways to speed up the drywall installation process without compromising quality: Hire Experienced Professionals: Skilled drywall installers can complete the work faster and often avoid mistakes that add time to the project. Use Fast-Drying Compound: For projects on a tight timeline, fast-setting joint compound can be a helpful alternative to traditional mudding. Ensure Proper Ventilation and Heating: Using fans and heaters can help speed up drying times for mudding in colder, more humid basements. Prepare Your Space in Advance: Clearing out the work area and ensuring easy access to tools and materials can help installers work more efficiently. Wrapping Up Drywalling your basement is a significant step in any basement renovation, transforming a raw space into a usable, inviting part of your home. While it’s a process that takes time, the result is well worth it. By working with experienced professionals, you can achieve a polished look that’s both durable and visually appealing, adding long-term value to your home. If you’re planning a basement renovation in Regina, partnering with professionals like Regina Drywallers can make all the difference. With skilled installers who understand the unique needs of local homes, you can count on a high-quality finish that’s completed efficiently. Get in touch with us to discuss your basement drywall needs and to receive a personalized estimate for your project.
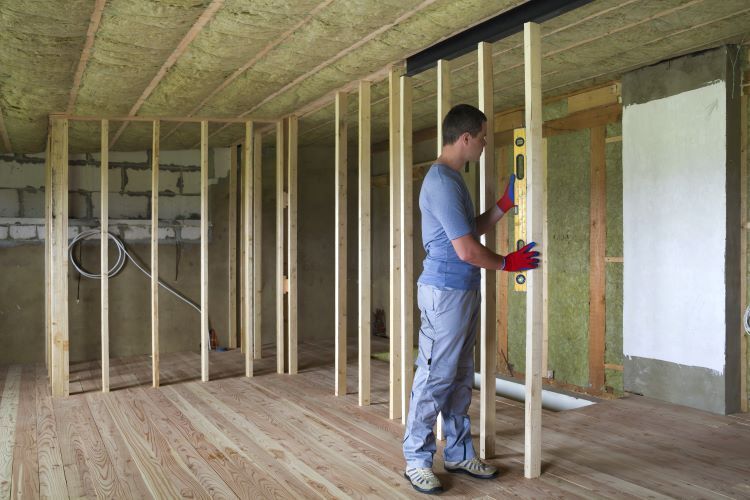
When it comes to building or renovating with drywall, one of the key decisions you’ll need to make is choosing between metal and wood framing. Both options have their own unique advantages and potential drawbacks, making it important to select the material that best suits your specific project needs. At Regina Drywallers, we know that the right framing can make all the difference in the stability, durability, and overall quality of your drywall installation . In this article, we’ll break down the differences between metal and wood framing , exploring the benefits and challenges of each to help you make an informed decision. 1. Durability and Strength Metal Framing One of the primary benefits of metal framing is its strength and durability. Made from steel, metal studs are resistant to warping, shrinking, and splitting, making them ideal for projects where long-term structural integrity is essential. This makes metal framing a popular choice for commercial buildings and other structures that require enhanced durability. Metal framing is also resistant to pests like termites and rot, which are common problems with wood framing, especially in areas with high humidity or moisture. If your project is in a basement, garage, or any space exposed to damp conditions, metal framing could be the better option. Wood Framing Wood framing, on the other hand, is incredibly sturdy and can hold up well in many residential construction projects. While wood is susceptible to warping and rotting over time, especially when exposed to moisture, it is still a tried-and-true material that has been used in construction for centuries. Many contractors are familiar with working with wood framing, making it a popular choice for homes and smaller-scale projects. However, in areas like Regina, where seasonal moisture and temperature fluctuations are common, wood framing may require more maintenance over time. 2. Cost Considerations Wood Framing In most cases, wood framing is less expensive than metal framing. The upfront cost of wood materials tends to be lower, which makes it a more budget-friendly option for many homeowners and builders. Additionally, because wood is a traditional material, the labor costs associated with wood framing are often lower, as most contractors are highly experienced in its use. Metal Framing While metal framing is typically more expensive than wood, it can provide long-term cost savings due to its durability and low maintenance requirements. Metal framing also eliminates the need for additional pest control measures, as it is resistant to termites and other wood-boring insects. This can help reduce maintenance costs over time, making it a good investment in certain scenarios. 3. Ease of Installation Wood Framing Wood framing is generally easier to work with, particularly for those who are DIY enthusiasts or builders who are familiar with traditional construction techniques. Wood is easier to cut, shape, and modify on-site, making it ideal for projects that require customization or changes during construction. Additionally, wood framing is easier to attach materials like drywall, insulation, and electrical components to, which can speed up the overall installation process. Metal Framing Metal framing, while durable, requires specialized tools and techniques for installation. Cutting metal studs requires more effort than cutting wood, and attaching drywall to metal framing involves using specific types of fasteners. However, once installed, metal framing can save time in the long run due to its strength and precision, as it doesn’t expand or contract with temperature changes. For larger commercial projects or those requiring complex architectural designs, metal framing can provide greater accuracy and consistency. 4. Environmental Impact Wood Framing Wood is a renewable resource, making it a more eco-friendly choice when sourced from sustainably managed forests. Many builders prefer wood for its natural aesthetic and the fact that it can be recycled or repurposed. However, deforestation and the carbon footprint of lumber production can have negative environmental impacts if the wood is not sourced responsibly. Metal Framing While metal is not a renewable resource, it is highly recyclable, and steel framing often contains a high percentage of recycled materials. Steel production does have a higher energy cost compared to wood, but its durability and long lifespan can offset this in the long term. Metal framing’s resistance to fire, termites, and other damage also means fewer repairs and replacements, reducing waste over time. 5. Fire Resistance Metal Framing One of the most significant advantages of metal framing is its fire resistance. Steel does not burn, making metal framing a safer option in areas where fire safety is a priority. This makes metal framing particularly valuable in commercial settings or multi-family residences, where stringent fire safety regulations may apply. Wood Framing While wood framing can be treated with fire-retardant chemicals, it is inherently more vulnerable to fire than metal. In residential applications, the fire resistance of wood framing may be less of a concern, especially if the structure meets local building codes and includes proper fireproofing measures. 6. Soundproofing and Insulation Wood Framing Wood has natural insulating properties, which can make it a better choice for soundproofing and thermal insulation. It absorbs sound and helps regulate indoor temperatures, making wood framing a popular choice for homes and spaces where comfort and privacy are key considerations. Metal Framing Metal studs, on their own, are not great sound insulators. However, they can be combined with sound-dampening materials like insulation and resilient channels to improve soundproofing. If sound control is a priority in your project, additional materials will need to be installed alongside metal framing to achieve the desired result. Which Framing Material is Right for Your Project? Ultimately, the decision between metal and wood framing depends on your project’s specific needs. For residential projects where cost, ease of installation, and soundproofing are priorities, wood framing is often the best choice. However, for commercial buildings, areas with high moisture levels, or projects requiring enhanced fire resistance and durability, metal framing may be the better option. At Regina Drywallers , we have experience working with both metal and wood framing and can help you determine the right material for your project. Whether you’re building a new home, renovating a commercial space, or simply upgrading your current property, our team of experts is here to provide top-quality drywall installation and framing services. Contact us today to discuss your project and learn how we can help you achieve the perfect result with the right framing solution!
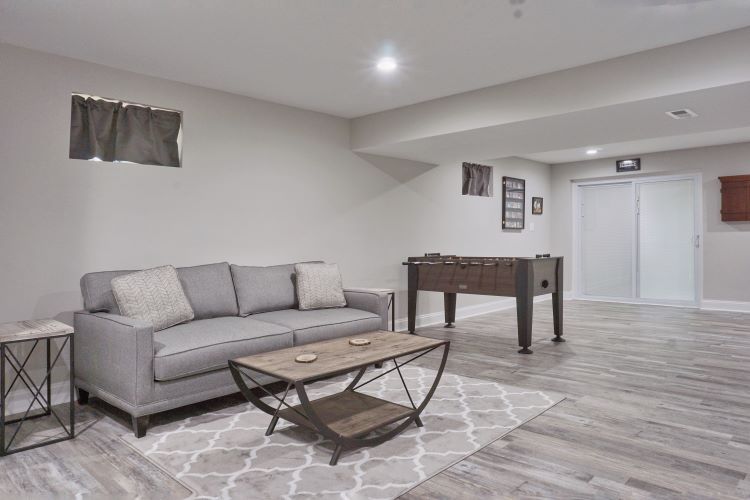
Drywall is a popular choice for interior walls in homes and commercial spaces due to its durability, ease of installation, and cost-effectiveness. However, like any material, drywall requires regular maintenance to keep it looking pristine and to extend its lifespan. At Regina Drywallers , we understand the importance of proper drywall maintenance , and we’re here to share some essential tips to help you keep your walls in perfect condition. 1. Regular Cleaning Dust and dirt can accumulate on drywall surfaces, leading to unsightly marks and stains over time. Regular cleaning can help maintain the appearance of your walls: Use a Soft Cloth or Duster: A soft, dry cloth or a duster can effectively remove dust from your walls without scratching the surface. Mild Cleaning Solutions: For stubborn stains, mix a small amount of dish soap with water and use a sponge to gently scrub the area. Avoid using harsh chemicals, as they can damage the drywall. 2. Inspect for Damage Regular inspections of your drywall can help identify issues before they become significant problems. Look for: Cracks and Holes: Small cracks may develop over time due to settling or temperature changes. Addressing these early can prevent larger repairs later. Water Damage: Check for signs of water stains or soft spots, which could indicate leaks or moisture problems. Addressing moisture issues promptly is critical to prevent mold growth. 3. Repairing Damage Promptly If you notice any damage, it’s essential to address it as soon as possible. Here’s how to repair common drywall issues: Small Cracks: For hairline cracks, use a joint compound to fill in the gaps. Once dry, sand the area lightly and repaint. Holes: For small holes, use a patching compound or drywall patch. For larger holes, you may need to cut a new piece of drywall, secure it in place, and then finish it with joint compound. Water Damage: If you find water damage, determine the source of the leak, repair it, and then replace the damaged drywall. This may require professional assistance if the damage is extensive. 4. Use Proper Wall Decor Techniques When hanging pictures or shelves, use the correct techniques to avoid damaging your drywall: Anchors and Brackets: Use wall anchors or brackets for heavier items to distribute the weight and prevent holes from forming. Avoid Overloading: Be mindful of the weight of items you hang. Overloading a section of drywall can lead to sagging or cracking. 5. Control Humidity Levels Humidity can significantly impact the condition of your drywall. Here’s how to manage humidity: Use Dehumidifiers: In areas prone to high moisture, such as basements, consider using a dehumidifier to maintain a comfortable humidity level. Proper Ventilation: Ensure proper ventilation in areas like kitchens and bathrooms to reduce moisture buildup. Use exhaust fans when cooking or showering. 6. Repaint When Necessary Repainting your walls not only enhances the aesthetics of your space but also adds a protective layer to your drywall. Here’s when and how to repaint: Touch Up Scratches: For minor scratches or scuffs, consider using touch-up paint to maintain a clean look. Full Repaint: If your walls look dull or stained, it may be time for a fresh coat of paint. Choose high-quality paint designed for drywall, and consider a washable finish for easier cleaning in the future. 7. Consider Professional Maintenance For extensive repairs or maintenance tasks, consider hiring professionals. Regina Drywallers can assess the condition of your drywall and perform any necessary repairs or maintenance efficiently. Professional maintenance ensures that any underlying issues are addressed, providing peace of mind for homeowners. Conclusion Proper drywall maintenance is essential for keeping your walls looking their best and prolonging their lifespan. Regular cleaning, prompt repairs, and monitoring humidity levels can make a significant difference in maintaining the integrity of your drywall. If you need assistance with drywall repairs or maintenance, don’t hesitate to reach out to Regina Drywallers . Our experienced team is here to help you keep your walls in perfect condition, ensuring your home remains beautiful and functional for years to come. Contact us today for all your drywall needs!
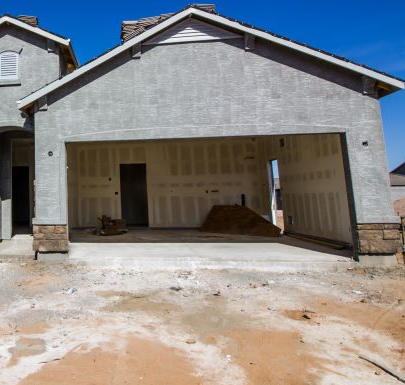
If you're looking to improve the look and functionality of your garage, finishing the drywall is a great place to start. Not only does it enhance the overall appearance, but it also provides insulation , fire resistance, and additional protection to the space. Whether you're using your garage for storage, a workshop, or as an extension of your living space, properly finishing the drywall can make a huge difference. At Regina Drywallers, we specialize in professional drywall services , and in this guide, we’ll walk you through the step-by-step process of finishing drywall in your garage. Step 1: Gather Your Materials and Tools Before you begin, ensure you have all the necessary materials and tools. Proper preparation will save you time and ensure a smoother drywall finishing process. Materials You’ll Need: Drywall sheets Joint compound (mud) Drywall tape (paper or mesh) Drywall screws Sandpaper (120-grit for smoothing) Primer and paint (optional) Tools: Utility knife Drywall screw gun or drill Mud pan and drywall knife Taping knife Sanding block or drywall sander Measuring tape Ladder or scaffold (if needed) Step 2: Install the Drywall Sheets The first step in finishing drywall is to install the drywall sheets properly. Start by measuring the walls and cutting the drywall sheets to size. Key Tips for Installing Drywall: Measure twice, cut once. Ensure the sheets fit the space correctly, especially around windows, doors, and electrical outlets. Attach the drywall sheets to the garage studs using drywall screws. Place screws every 12–16 inches along the edges and centers of the drywall sheets. Use a screw gun to avoid overdriving the screws into the drywall, which can cause damage. Once all the drywall sheets are in place, the next step is to focus on covering the joints and seams. Step 3: Tape the Drywall Seams Taping the seams between drywall sheets is a crucial step to create a smooth, seamless finish. You have the option to use either paper tape or mesh tape. Both work well, but paper tape is more durable, while mesh tape is easier to apply. How to Apply Drywall Tape: Apply a thin layer of joint compound (mud) over the seams using a taping knife. Press the tape firmly over the joint, making sure it lies flat and straight. Smooth out any bubbles or wrinkles using the taping knife. Apply a thin layer of mud over the tape, feathering the edges to blend the seam into the drywall. Repeat this process for all joints, corners, and any areas where drywall sheets meet. Step 4: Apply the First Coat of Joint Compound After taping, it’s time to apply the first coat of joint compound over the seams, screw holes, and any imperfections in the drywall. The goal is to create a smooth, even surface that’s ready for sanding. How to Apply Joint Compound: Using a drywall knife, spread a thin layer of joint compound over the taped seams, screw holes, and corners. Feather the edges of the compound to ensure a smooth transition between the drywall and the joints. Let the first coat dry completely, which may take several hours to overnight, depending on the temperature and humidity in your garage. Step 5: Apply Additional Coats of Joint Compound Once the first coat has dried, it’s time to apply additional coats of joint compound. Typically, two to three coats are required for a perfectly smooth finish. Additional Coats: After the first coat has dried, lightly sand the joints using fine-grit sandpaper (120-grit) to remove any bumps or ridges. Apply a second coat of joint compound, spreading it slightly wider than the first coat to further smooth and feather the edges. Let the second coat dry completely, then sand again. Repeat this process for the third coat, if necessary, making sure each layer is thinner and smoother than the previous one. The goal is to make the seams and screw holes invisible, with the surface completely even and ready for painting. Step 6: Sand the Drywall Once all the coats of joint compound are dry, it’s time to sand the drywall. This is an important step to ensure a smooth, even surface. Sanding Tips: Use a sanding block or a drywall sander for large areas. For smaller areas, a sanding sponge works well. Sand lightly in a circular motion to blend the joint compound with the rest of the drywall surface. Be careful not to sand too aggressively, as this can damage the drywall or leave uneven patches. After sanding, wipe down the walls with a damp cloth to remove any dust. Step 7: Prime and Paint (Optional) At this point, your drywall is finished, and you can choose to prime and paint the walls if desired. Priming the drywall is recommended before painting to seal the surface and ensure even paint coverage. Priming and Painting: Apply a coat of drywall primer using a roller, covering the entire surface evenly. Once the primer is dry, apply your chosen paint color to give your garage a clean, finished look. Step 8: Final Inspection Before considering the project complete, do a final inspection of the drywall to ensure all seams are smooth, there are no visible screw holes, and the surface is ready for painting or any further treatments. If you notice any imperfections, go back and apply a light layer of joint compound and sand again. Conclusion Finishing drywall in your garage is a rewarding project that enhances the space's appearance, insulation, and fire resistance. While it’s a multi-step process, taking your time and following each step carefully will result in a professional-looking finish. If you’d rather leave the job to the professionals, Regina Drywallers offers expert drywall installation and finishing services to ensure your garage looks its best. Whether you're looking to create a more polished workspace, protect your walls, or improve your home's insulation, finishing the drywall in your garage is a great investment. Contact Regina Drywallers today to learn more about our services and how we can help with your next drywall project!
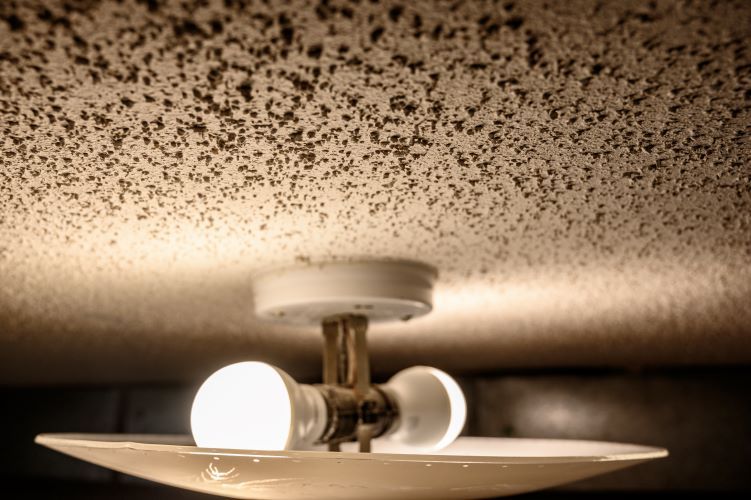
Popcorn ceilings, once a popular design trend, are now considered outdated by most homeowners. Their bumpy texture can make rooms feel older, and they can be difficult to clean. If you’re considering removing popcorn ceilings in your home, you’re not alone—many homeowners in Regina are opting for smoother, modern ceiling finishes. But before diving into this renovation project, there are several important factors to consider to ensure the process goes smoothly and safely. 1. Asbestos Testing Before removing any popcorn ceiling, the most critical consideration is whether it contains asbestos. Many homes built or renovated before the 1980s used materials that contained asbestos, which can be hazardous if disturbed. Inhaling asbestos fibers can lead to severe respiratory issues, including lung disease and cancer. If your home was built before 1990, it’s essential to test the ceiling for asbestos before proceeding with removal. Professional testing is recommended to determine whether asbestos is present. If it is, you’ll need to hire a certified asbestos removal specialist to handle the project safely. 2. Level of Mess Removing popcorn ceilings is a messy job. The texture, when scraped off, creates a significant amount of dust and debris. It’s important to take steps to protect your furniture, floors, and belongings before starting. Covering the floor with plastic sheeting and moving furniture out of the room can help keep the mess contained. Additionally, wearing protective gear like goggles, a mask, and gloves is essential to protect yourself from dust and debris during the removal process. Hiring professionals, like Regina Drywallers, ensures the cleanup is handled properly, saving you time and hassle. 3. Prep Work and Tools Needed Proper preparation is crucial for successful popcorn ceiling removal. The ceiling texture can be scraped off more easily when wet, so the process typically involves spraying the ceiling with water to soften the material. Tools commonly used for this task include a wide scraper or putty knife, a sprayer, and protective gear. If you plan to tackle this project yourself, be prepared for the amount of physical labor it requires. Scraping off the texture can be tiring, especially for larger rooms. On the other hand, hiring a professional drywall team ensures the job is done efficiently, with the proper tools and experience. 4. Potential Ceiling Damage While scraping off popcorn texture may seem straightforward, there’s a risk of damaging the underlying drywall if not done carefully. Popcorn ceilings were often used to hide imperfections in the ceiling, such as uneven surfaces, poorly finished seams, or cracks. Once the popcorn texture is removed, these flaws may become visible. In some cases, you may find that the ceiling requires patching or additional repairs before it can be refinished. Professional drywall contractors are skilled at identifying and fixing any underlying issues that may arise during the removal process, ensuring a smooth, polished finish. 5. Refinishing the Ceiling After the popcorn ceiling is removed, the next step is to decide how you want to refinish the ceiling. Popular options include a smooth, flat finish or a lightly textured surface, such as a knockdown texture. Each option provides a clean, modern look, but it’s important to consider the time and cost involved in refinishing. A smooth finish requires careful sanding and often a few coats of joint compound to get the surface perfectly even. Light texturing, on the other hand, may hide minor imperfections more easily while still providing a contemporary appearance. Either way, hiring a professional drywall contractor ensures a high-quality result. 6. Time and Cost The cost of popcorn ceiling removal varies depending on factors like the size of the room, the condition of the ceiling, and whether asbestos is present. In general, the process can take several days from start to finish, especially if extensive prep work or repairs are needed. Hiring a professional drywall company can save you time and ensure the job is done correctly the first time. While it may be tempting to DIY the removal to save on costs, the expertise of a professional ensures that your ceiling will look great without the stress of a DIY project gone wrong. 7. Increased Home Value Removing popcorn ceilings is not only about aesthetics but also about adding value to your home. Modern, smooth ceilings are more appealing to potential buyers and can significantly increase the resale value of your home. Popcorn ceilings are often seen as outdated, and removing them can make a home feel more updated and well-maintained. If you plan to sell your home in the future, investing in popcorn ceiling removal could pay off by making your property more attractive on the market. Conclusion Removing popcorn ceilings can be a game-changer for updating your home, but it’s important to consider all aspects of the project before starting. From asbestos testing to refinishing, popcorn ceiling removal is a task that requires careful planning and expertise. At Regina Drywallers , we offer professional popcorn ceiling removal services that ensure safety, efficiency, and a flawless finish. Whether you’re dealing with asbestos concerns or simply want to modernize your space, we have the experience to guide you through every step of the process. Contact us today to discuss your project and transform your ceilings with confidence. This article provides essential considerations for homeowners contemplating popcorn ceiling removal, emphasizing the importance of preparation, professional services, and the impact on home value.